ICCP Offshore Wind turbine protection
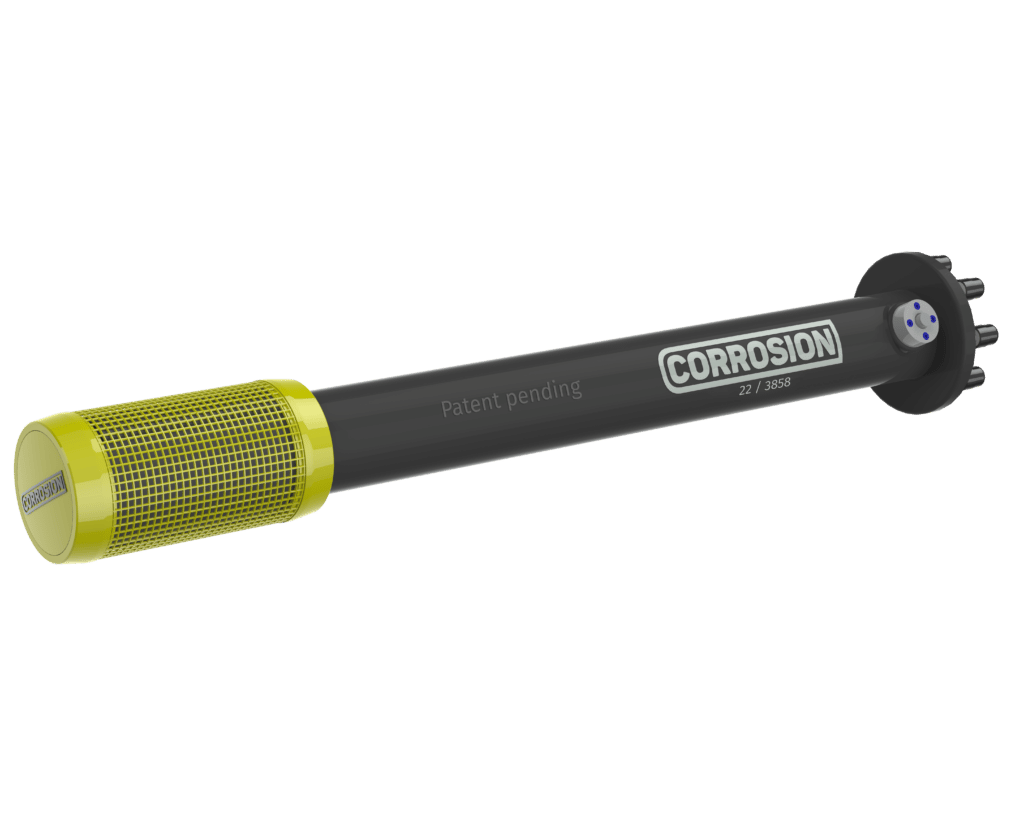
ICCP technology and wind turbine protection
CORROSION’s highly sophisticated Impressed Current Cathodic Protection
(ICCP) offshore wind system is the most cost-effective, easy-to-maintain and environmentally friendly solution on the market for the protection of offshore wind turbine foundations against corrosion.
Better performance at better value
While Galvanic Anode Cathodic Protection (GACP) systems operate on the natural driving force between two metals, our ICCP system uses a continuous external power source. CAPEX/OPEX calculations demonstrate that the ICCP-systems offer a far more economical solution for offshore wind turbine corrosion protection in the long term.
With this innovation, we respond to the developments in the market of offshore wind turbine corrosion protection, the increasingly challenging weather conditions, and the need to protect increasingly larger foundations, also known as the XX(X)L monopiles, in an environmentally friendly way.
The newly designed sustainable Impressed Current Cathodic Protection (ICCP) anode is already proving very effective on offshore turbine foundations worldwide. CORROSION’s new ‘slim fit’ anode design delivers the same quality and reliability as the current ICCP system, but is more efficient, versatile, and future proof.
The launch of our new ICCP anode design represents a huge step forward in efficiency in wind turbine corrosion protection. The anode head is more powerful and can therefore ‘impress’ more current. This makes it possible to protect the largest monopiles and reduce the amount of coating on monopiles to no coating at all.
In addition, this design offers a unique and new installation option. Besides to mounting on a TP and boat landing ladder, this anode can also be installed on the foundation itself. Which leads to big savings in time and money in wind turbine protection
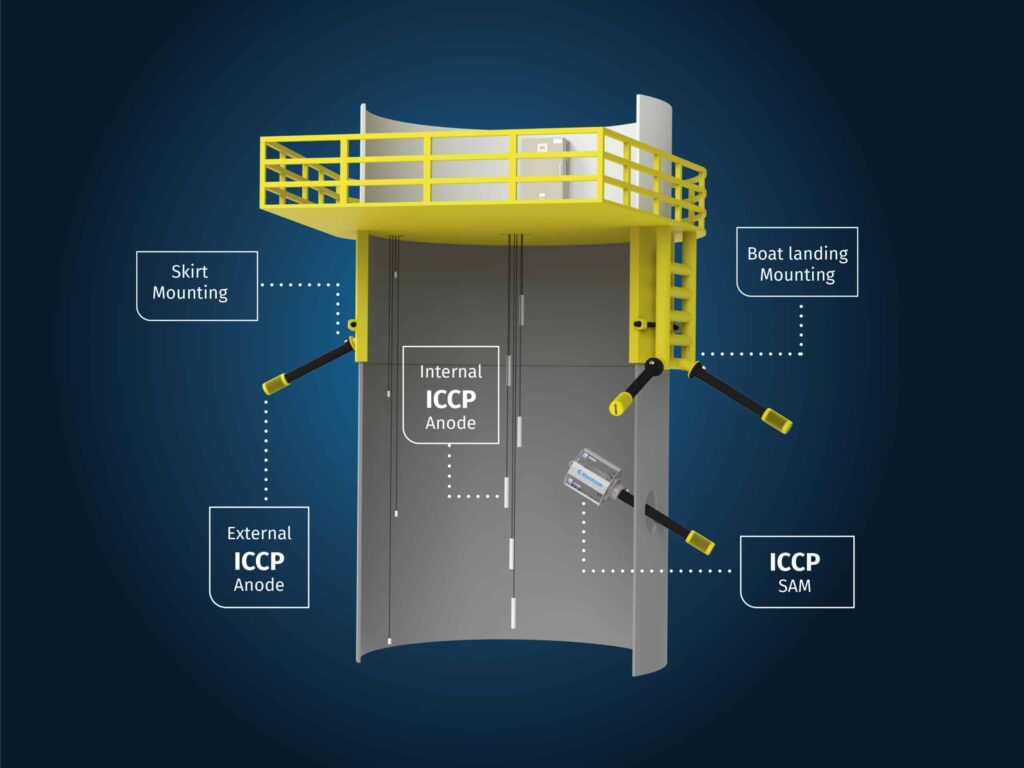
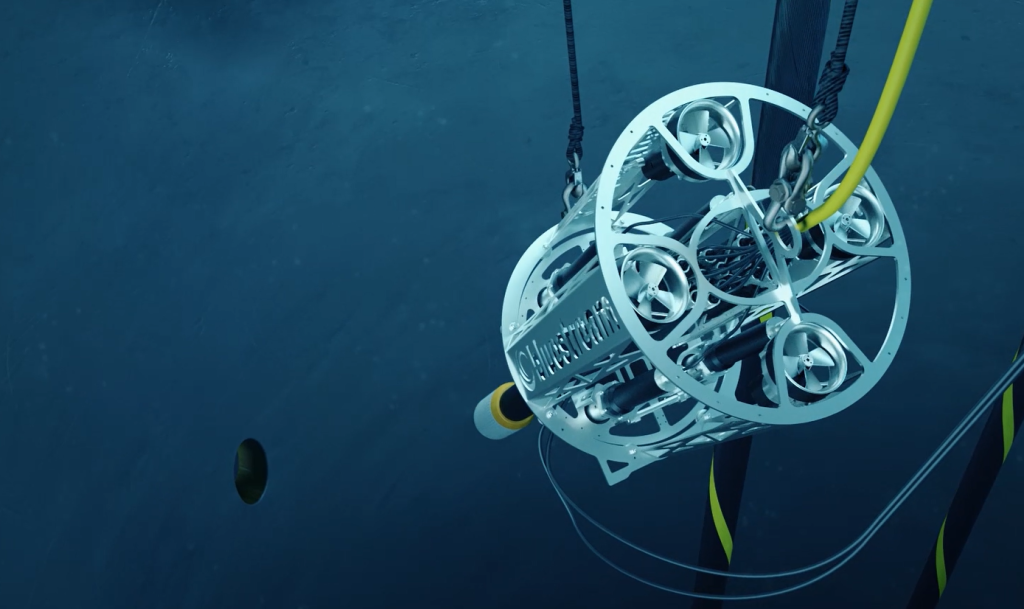
ICCP-SAM
Discover CORROSION’s and BLUESTREAM pioneering installation method, developed in collaboration by the 2 R&D departments supported by CORROSION’s laboratory, for ICCP anodes offshore. THE ICCP-SAM!
Learn more about the registered process, where anodes are installed via the inside of a monopile using propellered installation equipment and advanced techniques for optimal corrosion protection.
CORROSION’s pioneering installation method, developed in collaboration with BLUESTREAM, has been widely recognized and embraced by the industry and DNV approved. This revolutionary process offers the industry both a CAPEX and OPEX friendly solution. It allows savings on an installation vessel and provides freedom in the installation window. Supporting a better carbon footprint by not using extra secondary steel and it gives the owner even more design flexibilities.
Installation takes place offshore from the inside of a monopile. The ICCP anode is connected to a thruster-driven installation tool, ensuring efficient and accurate installation including measuring equipment for full reporting. Using access points/manhole in the ATP, the connected assembly is lowered into place. Once at the desired location, the anode is placed horizontally for optimum effectiveness and installation.
A pre-created oval shaped hole in the monopile enables seamless installation of the anode. A pressure plate or clamp secures the anode to the foundation, ensuring stability and longevity. Reversed installation is possible to interchange anodes during lifetime or for lifetime extension.
Another method is to mount the ICCP anode from the outside. This approach uses a special tool developed by BLUESTREAM, which has proven itself in the installation of Mudline reference cells in offshore wind farms. When mounted from the outside, a dielectric shield is used on the foundation instead of a standoff. More information on this pioneering installation method and its benefits can be found at here.
Thanks to CORROSION and BLUESTREAM’s innovative approach, offshore installations can now benefit from enhanced corrosion protection and streamlined installation processes.
BLUESTREAM is a Dutch Offshore company specialized in difficult offshore diving and ROV operations in the Oil/Gas and Wind industry. BLUESTREAM is part of OEG Offshore.
Durability and longevity
What’s more, traditional technologies require large quantities of heavy sacrificial anodes to meet the offshore foundation design life of over 25 years. In contrast, CORROSION’s ICCP system requires only a limited number of ICCP anodes and sensors to work effectively for well over 25 years, which is in excess of the initial design life of the wind turbines. As a result, the same system can continue to be used even in the event of the offshore wind farm lifetime being extended.
A further advantage of our ICCP wind systems is that they are equipped with a standard feature to take data readings and make adjustments at the touch of a button from an offshore wind farm control center rather than having to do so on location – something particularly important given the hard-to-reach locations of many offshore wind farms. System performance is monitored, and a warning is triggered if any of the values are too high or too low.
For GACP systems, regular offshore campaigns are necessary to execute a performance and protection level check. These are both costly and time consuming.
Offshore Wind Projects
Protecting over 2.300 foundations, and counting
Project name | Foundation | |
Albatros | 16 | Monopile |
Albatros | 16 | Monopile |
Alpha Ventus | 6 | Tripod |
Arkona Becken | 60 | Monopile |
Baltic Eagle | 50 | Monopile |
Baltic II Substation | 1 | Jacket |
Belwind II | 50 | Monopile |
Borkum West II | 1 | Jacket |
Borkum west II – Phase II | 32 | Monopile |
Borssele III & IV | 77 | Monopile |
Borssele V | 2 | Monopile |
Butendiek | 80 | Monopile |
Changle A | 26 | Jacket |
Changle A Substation | 1 | Jacket |
Changle C | 14 | Jacket |
DanTysk | 80 | Monopile |
DanTysk Substation | 1 | Jacket |
DanTysk OAP Substation | 1 | Jacket |
Deutsche Bucht | 31 | Monopile |
Galloper | 56 | Monopile |
Global Tech | 80 | Tripod |
Global Tech Substation | 1 | Jacket |
Greater Gabbard | 140 | Monopile |
Hohe See | 71 | Monopile |
Hollandse kust | 70 | Monopile |
Horns Rev III | 49 | Monopile |
Kaskasi Substation | 1 | Monopile |
Kaskasi II | 38 | Monopile |
Les Eoliennes Flottantes du Golf du Lion | 4 | Monopile |
Luchterduinen | 43 | Monopile |
Meerwind | 80 | Monopile |
Meerwind Substation | 1 | Jacket |
Merkur | 66 | Monopile |
Seamade (Seastar) | 30 | Monopile |
Seamade (Mermaid) | 28 | Monopile |
Northwester II | 23 | Monopile |
Northwester II Substation | 1 | Monopile |
Noshiro Port | 21 | Monopile |
Rentel | 42 | Monopile |
Riffgat | 30 | Monopile |
Riffgat Substation | 1 | Jacket |
Saint Nazaire | 80 | Monopile |
Sandbank | 72 | Monopile |
Triton Knoll | 90 | Monopile |
Veja Mate | 67 | Monopile |
Xinghua Bay Substation | 1 | Monopile |
Yunlin | 80 | Monopile |
Offshore Wind Projects
Protecting over 2.300 foundations, and counting
Project name | Foundation quantity | Foundation type | ICCP Protection | Commissioning date | |
Albatros | 16 | Monopile | Internal | 09-01-2020 | |
Alpha Ventus | 6 | Tripod | External | 27-04-2010 | |
Arkona Becken | 60 | Monopile | Internal | 01-01-2019 | |
Baltic Eagle | 50 | Monopile | Internal | 30-09-2024 | |
Baltic II Substation | 1 | Jacket | External | 29-10-2015 | |
Belwind II | 50 | Monopile | External and Internal | 09-12-2010 | |
Borkum West II | 1 | Jacket | External | 03-07-2020 | |
Borkum west II – Phase II | 32 | Monopile | External and Internal | 03-07-2020 | |
Borssele III & IV | 77 | Monopile | External and Internal | 06-01-2021 | |
Borssele V | 2 | Monopile | External and Internal | 25-02-2021 |
Butendiek | 80 | Monopile | External | 04-08-2015 | |
Changle A | 26 | Jacket | External and Internal | 01-10-2021 | |
Changle A Substation | 1 | Jacket | External | 01-10-2021 | |
Changle C | 14 | Jacket | External | 01-10-2021 | |
DanTysk | 80 | Monopile | External | 30-04-2015 | |
DanTysk Substation | 1 | Jacket | External | 30-04-2015 | |
DanTysk OAP Substation | 1 | Jacket | External | 30-04-2015 | |
Deutsche Bucht | 31 | Monopile | External and Internal | 30-09-2019 | |
Galloper | 56 | Monopile | Internal | 03-04-2018 | |
Global Tech | 80 | Tripod | External | 02-09-2015 | |
Global Tech Substation | 1 | Jacket | External | 02-09-2015 | |
Greater Gabbard | 140 | Monopile | External | 07-08-2013 | |
Hohe See | 71 | Monopile | Internal | 01-11-2019 | |
Hollandse kust zuid | 140 | Monopile | External | 01-06-2023 | |
Horns Rev III | 49 | Monopile | External and Internal | 22-08-2019 | |
Kaskasi Substation | 1 | Monopile | External and Internal | 01-10-2022 | |
Kaskasi II | 38 | Monopile | External and Internal | 01-10-2022 | |
Les Eoliennes Flottantes du Golf du Lion | 4 | Monopile | External | 01-09-2023 | |
Luchterduinen | 43 | Monopile | External | 21-09-2015 | |
Meerwind | 80 | Monopile | External | 29-12-2014 | |
Meerwind Substation | 1 | Jacket | External | 29-12-2014 | |
Merkur | 66 | Monopile | External and Internal | 24-06-2019 | |
Seamade (Seastar) | 30 | Monopile | External and Internal | 15-12-2020 | |
Seamade (Mermaid) | 28 | Monopile | External and Internal | 15-12-2020 | |
Northwester II | 23 | Monopile | External and Internal | 14-05-2020 | |
Northwester II Substation | 1 | Monopile | External | 14-05-2020 | |
Noshiro Port | 20 | Monopile | External and Internal | 31-12-2022 | |
Rentel | 42 | Monopile | Internal | 31-12-2018 | |
Riffgat | 30 | Monopile | External and Internal | 07-03-2014 | |
Riffgat Substation | 1 | Jacket | External | 07-03-2014 | |
Saint Nazaire | 80 | Monopile | External and Internal | 31-12-2022 | |
Sandbank | 72 | Monopile | External and Internal | 25-01-2017 | |
Triton Knoll | 90 | Monopile | External and Internal | 01-01-2022 | |
Veja Mate | 67 | Monopile | Internal | 31-05-2017 | |
Xinghua Bay Substation | 1 | Monopile | External | 01-01-2017 | |
Yunlin | 80 | Monopile | External and Internal | 31-03-2022 |
GACP systems have a very significant carbon footprint long before they are even installed on wind turbine foundations. The production process of aluminum – from extracting bauxite to producing a suitable aluminum alloy, in addition to that of heavy metal alloying elements such as Zinc – requires the transportation of metals over long distances, sometimes from one side of the world to another. Moreover, every additional sacrificial anode leads to the further depletion of resources such as aluminum and all the alloying elements.
Post-installation, GACP systems release tons of potentially harmful metals into the world’s seas and oceans. A 1,000-megawatt windfarm with 100 monopiles requires an average of 1000 tons of aluminum anodes, in addition to heavy metal zinc alloying element of approximately 50 tons – all of which will dissolve in the seawater and affect the marine life.
In comparison, for the very same 1,000-megawatt windfarm, CORROSION’s ICCP system anodes only require a 750-gram coating of Metal Mixed Oxide (MMO). These oxides are made of precious metals such as Iridium, Platinum, Ruthenium and not of heavy metals.
This means around 60,000 times less zinc and 1.5 million times less aluminum is emitted into marine environment than our ICCP system than with traditional sacrificial anodes. More information can be found in our whitepaper ‘ICCP vs GACP’.
Downloads
Downloads
FAQ
Preventative maintenance should in general be carried out on offshore wind turbines two or three times a year. The frequency of maintenance of offshore wind turbine foundations depends on whether the turbines are protected using an Impressed Current Cathodic Protection or a (ICCP) system or a Galvanic Anode Cathodic Protection (GACP) system, with the latter requiring more frequent checks.
The average design life of wind turbines is approximately 25 years, depending on environmental conditions such as wind speed. Turbine foundations are designed to last longer, taking into account the time of installation and disassembly